Why Lean Management? The Advantages of Lean Thinking for Your Business
- Shawn Lin
- Apr 9, 2024
- 12 min read
Updated: Apr 11, 2024
1. Introduction

In the rapidly evolving business landscape of Southeast Asia, companies constantly search for strategies to stay ahead of the curve, enhance efficiency, and deliver unparalleled customer value. Enter Lean Management, a systematic approach that has transformed organizations worldwide by emphasizing waste reduction, value creation, and continuous improvement. Originating from the manufacturing floors of Toyota in Japan, Lean principles have transcended industry boundaries, offering a versatile framework for operational excellence.
Lean Thinking is not just a set of tools; it's a mindset that encourages businesses to look at their processes through the lens of value from the customer's perspective. By doing so, companies can identify non-value-adding activities and eliminate them, leading to streamlined operations, enhanced product quality, and improved customer satisfaction. In the competitive markets of Southeast Asia, where diversity, rapid change, and innovation are the norms, Lean Management stands as a beacon for businesses aiming to achieve sustainable growth and a competitive edge.
This blog post delves into the core advantages of adopting Lean Thinking for your business, offering insights into how this philosophy can transform operations, reduce costs, and elevate the customer experience. Whether you're a small startup or an established enterprise in the SEA region, understanding and implementing Lean principles can unlock new levels of operational efficiency and business success. Join us as we explore the transformative potential of Lean Management and how it can be the catalyst your business needs to thrive in today's dynamic market environment.
2. Understanding Lean Management
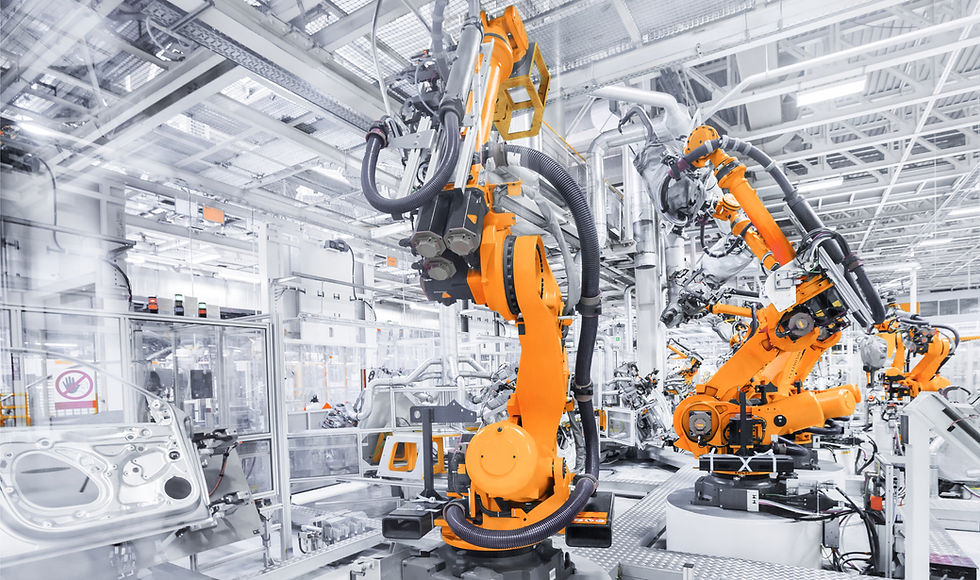
Lean Management is a holistic approach to running a business that emphasizes creating more value for customers with fewer resources. It originated in the mid-20th century with the Toyota Production System, a methodology designed to eliminate waste and improve efficiency in manufacturing processes. However, Lean has since evolved to be applicable across various sectors, proving its versatility and effectiveness in enhancing operational performance.
2.1 Definition and Origins of Lean Management
At its core, Lean Management is defined by its focus on maximizing customer value while minimizing waste. This means creating more value for customers with fewer resources. The origins of Lean can be traced back to the manufacturing industry in Japan, specifically to the Toyota Production System, which sought to streamline production, reduce costs, and increase quality. Toyota’s success with this system garnered international attention and led businesses worldwide to adopt its principles.
2.2 Core Principles of Lean Thinking

Lean Thinking is guided by five core principles:
Value: Define value from the customer's perspective. Understand what aspects of your service or product the customer is willing to pay for.
Value Stream: Identify all the steps in the value stream for each product or service, eliminating steps that do not create value.
Flow: Ensure that the value-creating steps occur in a tight sequence so the product or service flows smoothly toward the customer.
Pull: Instead of pushing products on customers, let customer demand pull the product through the manufacturing and delivery processes.
Perfection: Continually pursue perfection by refining processes, enhancing efficiency, and eliminating waste in all forms.
2.3 How Lean Management Differs from Traditional Management Practices
Unlike traditional management practices that often prioritize maximizing output and reducing costs through economies of scale, Lean Management focuses on value creation and waste elimination. Traditional models may lead to overproduction, excess inventory, and inefficiencies, whereas Lean promotes a customer-centric approach, ensuring that every process adds value and meets customer needs. This shift in focus from a push-based production model to a pull-based one, driven by actual customer demand, represents a fundamental change in how businesses operate and compete.
Lean Management also empowers employees at all levels to participate in continuous improvement efforts, contrasting with traditional top-down decision-making structures. This empowerment leads to a more engaged workforce, capable of identifying inefficiencies and innovating solutions, further driving the organization towards operational excellence.
By understanding the principles and practices of Lean Management, businesses in the SEA region can adapt this approach to navigate the complexities of today’s markets, streamline operations, and enhance competitiveness. Lean is not a one-size-fits-all solution but a flexible framework that organizations can tailor to their specific context and challenges, paving the way for sustainable growth and long-term success.
3. The Advantages of Lean Thinking for Your Business

Adopting Lean Thinking can significantly transform how a business operates, leading to enhanced performance, reduced costs, and improved customer satisfaction. Below, we delve into the key advantages of integrating Lean principles into your business operations, especially within the dynamic and diverse business landscape of the Southeast Asia (SEA) region.
3.1 Waste Reduction
One of the foundational goals of Lean Management is the identification and elimination of waste—activities that consume resources but do not add value from the customer's perspective. There are seven types of waste Lean methodology targets: overproduction, waiting time, transportation, over-processing, inventory, motion, and defects. By systematically reducing these wastes, businesses can significantly lower costs, increase productivity, and ensure that resources are utilized as efficiently as possible.
Case Study: An SEA-based manufacturing firm implemented Lean techniques to streamline its production process. By identifying and eliminating unnecessary steps and reducing waiting times between operations, the company saw a 25% reduction in production costs and a 40% decrease in product lead time.
3.2 Enhanced Quality
Lean Thinking promotes continuous improvement (Kaizen) and quality control at every step of the production process. This approach not only reduces errors and defects but also fosters a culture of excellence and attention to detail.
Impact: Businesses adopting Lean can expect to see a marked improvement in the quality of their products and services, leading to higher customer satisfaction and repeat business. For instance, a software development company in the SEA region reduced its bug rate by 60% through iterative testing and feedback loops integrated into its Lean process.
3.3 Improved Customer Satisfaction
Lean Management focuses on value creation from the customer’s perspective, ensuring that products and services meet or exceed customer expectations. This customer-centric approach leads to enhanced satisfaction and loyalty.
Benefit: Companies that successfully implement Lean principles often report higher customer retention rates, increased referrals, and an improved brand reputation, as they are better able to respond to customer needs and market changes.
3.4 Increased Efficiency and Productivity
By streamlining processes and eliminating non-value-adding activities, Lean Management helps businesses operate more efficiently. This increase in efficiency often leads to higher productivity levels among employees, as they are able to focus on tasks that directly contribute to customer value.
Example: A retail chain in the SEA region applied Lean techniques to its supply chain and inventory management processes, resulting in a 30% improvement in inventory turnover and a 15% increase in sales due to better stock availability and variety.
3.5 Flexibility and Innovation
Lean encourages a culture of continuous improvement and innovation, enabling businesses to remain flexible and adaptable in the face of changing market demands and technological advancements.
Advantage: Organizations that embrace Lean are often more agile and innovative, able to pivot quickly in response to new opportunities or challenges. This agility is critical for sustained success in the fast-paced SEA market.
3.6 Cost Savings
The cumulative effect of waste reduction, improved quality, and increased efficiency often leads to significant cost savings. Lean businesses are able to do more with less, optimizing their resource utilization and reducing overhead costs.
Outcome: Companies implementing Lean Management have reported up to a 50% reduction in operational costs, with the savings reinvested into growth initiatives or passed on to customers in the form of competitive pricing.
The adoption of Lean Management offers a multitude of benefits for businesses looking to enhance their operational efficiency, reduce costs, and improve customer satisfaction. In the competitive and rapidly changing business environment of the SEA region, Lean Thinking provides a proven framework for achieving sustainable growth and market leadership. By focusing on value creation, continuous improvement, and waste elimination, companies can build a strong foundation for long-term success.
4. Implementing Lean Management in Your Business
The transition to Lean Management represents a significant shift in organizational culture and processes. However, the journey, while challenging, can lead to profound improvements in efficiency, customer satisfaction, and overall business performance. Here’s a step-by-step guide to begin implementing Lean principles in your business, tailored to the dynamic and diverse landscape of the Southeast Asia (SEA) region.
4.1 Steps to Begin the Lean Transformation

Commitment from Leadership: The Lean journey starts with a commitment from top management. Leadership must be fully engaged and willing to drive the change, setting clear visions and expectations.
Understand Lean Principles: Before implementation, it’s crucial that everyone in the organization understands the core principles of Lean and how they apply to your specific business context.
Map Your Value Stream: Identify your value streams by mapping out the entire process of delivering a product or service to the customer. This step helps in understanding the current flow and identifying areas of waste.
Create a Lean Implementation Plan: Based on the value stream mapping, develop a targeted implementation plan. Prioritize areas with the highest potential for improvement and set clear, measurable goals.
Empower Your Team: Lean management relies heavily on the insights and participation of frontline employees. Empower your team by providing training and encouraging their involvement in problem-solving and process improvements.
Implement and Test: Start small with pilot projects to test Lean practices. Use these pilots to learn and adapt before rolling out more broadly across the organization.
Iterate and Improve: Lean is about continuous improvement. Use feedback from your initial implementations to refine processes, and always be on the lookout for new ways to eliminate waste and add value.
4.2 Common Challenges and How to Overcome Them

Resistance to Change: Change can be difficult, and some employees may resist new ways of working. Overcome this by communicating the benefits of Lean clearly and involving employees in the process from the start.
Lack of Understanding: Misunderstandings about what Lean is and what it aims to achieve can derail your efforts. Address this by providing comprehensive training and clear examples of how Lean principles apply to your specific operations.
Sustaining Changes: Initial improvements can be challenging to maintain over the long term. Create a culture of continuous improvement by celebrating successes and integrating Lean practices into daily routines.
4.3 Tips for Sustaining Lean Practices in the Long Term

Leadership Involvement: Keep leadership actively involved in the Lean process, not just at the outset but as an ongoing practice.
Regular Training: Offer regular training and refresher courses to ensure that all employees remain engaged with Lean principles and practices.
Continuous Improvement Culture: Encourage a culture that sees every problem as an opportunity for improvement rather than a failure to be penalized.
Visibility of Metrics: Make key performance indicators (KPIs) and progress visible to all employees. This transparency helps maintain focus and motivation.
Employee Recognition: Recognize and reward contributions to Lean initiatives. This recognition can take many forms, from formal awards to simple acknowledgments in team meetings.
Implementing Lean Management is a journey that can lead to significant rewards for businesses in the SEA region. By following these steps, overcoming common challenges, and committing to continuous improvement, your business can achieve greater efficiency, improve customer satisfaction, and enhance overall competitiveness in the market.
5. Success Stories in the SEA Region
The adoption of Lean Management principles has led to transformative successes for many businesses in the Southeast Asia (SEA) region. These success stories serve as powerful testimonials to the efficacy of Lean thinking in improving operational efficiency, customer satisfaction, and overall business performance. Here, we highlight a few examples to inspire and guide companies considering their Lean journey.
5.1 Manufacturing Excellence: Electronics Manufacturer in Vietnam
A Vietnamese electronics manufacturer faced challenges with product defects and long lead times. By implementing Lean techniques, such as Kaizen for continuous improvement and 5S for workplace organization, the company achieved a dramatic reduction in defects by 70% and cut down lead times by 50%. This improvement not only enhanced customer satisfaction but also positioned the company as a competitive exporter in the international market.
5.2 Service Sector Innovation: Financial Services Firm in Singapore
A Singapore-based financial services firm applied Lean methodologies to streamline its customer service processes. Through value stream mapping, they identified several non-value-adding activities in their loan approval process. By eliminating these steps and optimizing the workflow, the firm reduced the loan approval time from 14 days to just 48 hours, significantly improving customer satisfaction and gaining a competitive edge in the market.
5.3 Healthcare Transformation: Hospital in Malaysia
A Malaysian hospital struggling with long patient wait times and inventory management issues turned to Lean principles for solutions. The implementation of just-in-time inventory management and process flow improvements led to a 30% reduction in patient wait times and a 20% decrease in inventory costs. These changes not only improved patient care but also increased the efficiency of hospital operations.
5.4 Retail Revolution: E-commerce Platform in Indonesia
An Indonesian e-commerce platform leveraged Lean management to enhance its logistics and customer service operations. By adopting a pull system for inventory management and streamlining their order fulfillment process, they achieved a 40% improvement in delivery times and a significant reduction in customer complaints related to shipping delays.
5.5 Startup Success: Tech Startup in Thailand
A tech startup in Thailand utilized Lean Startup methodologies, a variant of Lean thinking tailored for startups, to develop its mobile application. This approach allowed them to rapidly prototype, test, and refine their product based on customer feedback, leading to a highly successful launch with over a million downloads in the first six months.
These success stories from across the SEA region illustrate the versatility and impact of Lean Management across various industries, from manufacturing and healthcare to financial services and e-commerce. By adopting Lean principles, companies have not only achieved substantial operational improvements but also enhanced their competitive advantage in a rapidly evolving marketplace. These examples serve as a blueprint for other businesses seeking to embark on their own Lean transformation journey, highlighting the potential for significant gains in efficiency, customer satisfaction, and overall business performance.
6. Conclusion
The principles of Lean Management, rooted in maximizing value and minimizing waste, have demonstrated their versatility and impact across a broad spectrum of industries in the Southeast Asia (SEA) region. As evidenced by the success stories of various businesses—from manufacturing and healthcare to finance and e-commerce—Lean Thinking offers a comprehensive framework for operational excellence that is adaptable to the unique challenges and opportunities of the SEA market.
6.1 Key Takeaways
Waste Reduction: Lean Management's focus on eliminating non-value-adding activities leads to significant cost savings and efficiency improvements.
Enhanced Quality: A commitment to continuous improvement under Lean principles ensures that businesses can consistently enhance the quality of their products and services.
Improved Customer Satisfaction: By prioritizing value from the customer's perspective, businesses can achieve higher levels of customer satisfaction and loyalty.
Increased Efficiency and Productivity: Streamlining processes and empowering employees to contribute to improvement efforts result in heightened productivity and operational efficiency.
Flexibility and Innovation: Lean Management encourages a culture of innovation, allowing businesses to stay agile and responsive to market changes.
6.2 The Transformative Potential of Lean Thinking
Adopting Lean Management can transform businesses by fostering a culture of continuous improvement, operational excellence, and customer-centricity. The principles of Lean provide a solid foundation for businesses aiming to navigate the complexities of today’s competitive environment, especially in the dynamic and diverse SEA region. Companies that embrace these principles can look forward to not only surviving but thriving in the face of challenges, capitalizing on opportunities for growth and innovation.
6.3 Encouragement for the Lean Journey
The journey toward Lean Management is both a challenge and an opportunity. It requires commitment, flexibility, and a willingness to embrace change at all levels of the organization. However, the benefits—as demonstrated by numerous success stories—are profound and lasting. Businesses in the SEA region that embark on this journey can achieve remarkable improvements in performance, customer satisfaction, and competitive advantage.
Lean Management is more than just a set of tools or principles; it is a mindset that can fundamentally change how a business operates and engages with its customers. For companies in the Southeast Asia region looking to secure their place in a fast-paced and ever-evolving market landscape, Lean offers a pathway to achieving sustainable growth and operational excellence. Embracing the Lean philosophy can unlock the potential within your business to deliver exceptional value to your customers while driving efficiency and innovation across your operations.
7. Call to Action
The journey towards Lean Management and the continuous pursuit of improvement it embodies can significantly transform your business, making it more resilient, customer-focused, and efficient. If you're ready to start or enhance your Lean journey, consider the following steps to propel your business forward in the dynamic environment of the Southeast Asia (SEA) region.
7.1 Assess Your Current Operations
Begin with a thorough assessment of your current processes and operations. Identify areas where waste is evident, whether it’s in time, resources, or effort, and pinpoint opportunities for improvement. Understanding where you are today is the first step towards envisioning where you could be with Lean.
7.2 Engage Your Team
Lean Management is not a top-down directive; it thrives on the engagement and participation of employees at all levels. Involve your team in the Lean transformation process, offering training and education to equip them with the necessary skills and knowledge. Foster an environment where everyone feels empowered to suggest improvements and contribute to problem-solving.
7.3 Start Small, Think Big
Embarking on your Lean journey doesn’t mean overhauling your entire operation overnight. Start with small, manageable projects that allow you to see quick wins and learn from the process. These successes build momentum and buy-in from the team, setting the stage for larger-scale transformations.
7.4 Seek Expert Guidance
Consider partnering with a Lean Management consultant or expert who can provide outside perspective, share insights from other successful implementations, and guide you through the process. This expertise can be invaluable in avoiding common pitfalls and accelerating your progress.
7.5 Measure and Adjust
Implement mechanisms to track your progress, measure the impact of your Lean initiatives, and adjust your strategies based on what the data tells you. Continuous improvement means being willing to learn from every outcome and tweak your approach as needed.
7.6 Share Your Success
As you achieve milestones and see the benefits of your Lean initiatives, share these successes within your organization and with your customers. Highlighting these achievements can reinforce the value of Lean principles and motivate continued effort towards improvement.
In Conclusion
Your Lean Management journey is a strategic investment in the future of your business, promising not just improvements in efficiency and cost savings, but also enhancing customer satisfaction, employee engagement, and your overall competitive advantage. The dynamic and competitive landscape of the SEA region offers a fertile ground for businesses willing to embrace change and pursue excellence through Lean Thinking.
Are You Ready to Lean Into the Future?
Let this be the moment you decide to take the first step towards transforming your business with Lean Management. Remember, the journey is continuous, filled with learning and growth opportunities. With commitment, patience, and a focus on value, your business can reach new heights of success in the SEA region and beyond.
Sign up for a public programme today, or contact us for an in-house programme tailored just for your organisation.
Commenti